Краткий анализ ОВОС Завода по термическому обезвреживанию ТКО мощностью не менее 700000 тонн ТКО в год (д. Могутово Московской области)
В п. 2.2 ОВОС Завода по термическому обезвреживанию ТКО (д. Могутово Московской области) приводятся морфологический состав и теплотворная способность отходов. Согласно отчета АКХ им.Памфилова от 1995г. и отчета ОАО ЦБиОО от 2014г. теплотворная способность отходов составляет соответственно 8,3 и 11,1 МДж/кг, что обусловлено существенным различием морфологического состава. За 19 лет произошло существенное снижение в составе отходов пищевых отходов и бумаги и рост пластиковых отходов и отсева.
Однако в ОВОС не указан окончательный состав отходов, принятый в дальнейших расчетах.
В п. 2.6 ОВОС кратко описана технология процесса термического обезвреживания отходов.
В описании указывается, что на МСЗ поступают отходы, прошедшие предварительную сортировку, где отбираются полезные фракции и опасные компоненты. Таким образом на сжигание поступают «хвосты» сортировки. Имеется указание на снижение теплотворной способности и зольности сортированных отходов за счет извлечения части пластика и негорючих компонентов.
Процесс сжигания на колосниковых решетках протекает при температурах 850÷1260°С, средняя температура дымовых газов 900°С. Процесс горения на колосниковых решетках требует избытка воздуха. Топливо подается на решетку толкателем периодическими порциями. При такой подаче и слоевом сжигании одновременно протекают процессы сушки, пиролиза и горения. При пиролизе отдельных видов полимеров, входящих в состав пластиков, резины и текстиля, образуются в числе прочих ароматические и хлорсодержащие соединения. Наличие последних в дымовых газах, присутствие свободного кислорода, а также постепенное охлаждение дымовых газов от 900°С до 400°С при отдаче тепла трубной системе котла являются необходимым и достаточным условием синтеза диоксинов.
В условиях высоких температур и наличия кислорода происходит окисление тяжелых металлов, присутствующих в электронных компонентах и элементах питания, не удаленных из отходов на стадии сортировки. Мелкодисперсные оксиды с летучей золой выносятся из зоны горения дымовыми газами.
На МСЗ предусмотрена трехстадийная очистка газов.
1-я стадия – разложение оксидов азота путем впрыска в горячие дымовые газы раствора карбамида.
2-я стадия – сорбционная очистка от кислых газов, диоксинов и паров ртути путем распыления в дымовые газы мелкодисперсных порошков гидроксида кальция и активированного угля.
3-я стадия – механическая очистка дымовых газов на рукавных фильтрах. Фильтрующая поверхность из стеклоткани задерживает летучую золу с сорбированными на ней соединениями тяжелых металлов и диоксинами, мелкодисперсный порошок гидроксида кальция со связанными на нем кислыми соединениями, и мелкодисперсный порошок активированного угля с сорбированными на нем диоксинами и ртутью.
Продуктами сгорания «хвостов» ТКО являются:
- шлак в количестве 25÷30% от сожженного количества ТКО или 175÷210 тыс. т/год, 4-го класса опасности;
- зола и отработанные сорбенты в количестве 2,5÷3,0% от сожженного количества ТКО или 17,5÷21 тыс. т/год, 3-го класса опасности;
- очищенные дымовые газы в количестве 400 тыс. м3/час.
Указанное количество шлака характеризует очень высокую зольность сжигаемых отходов, что не согласуется с предварительной сортировкой и удалением негорючих компонентов.
В оригинальной технологии сжигания отходов Hitachi Zosen используется пятиступенчатая очистка дымовых газов. Схема МСЗ показана на рис.1
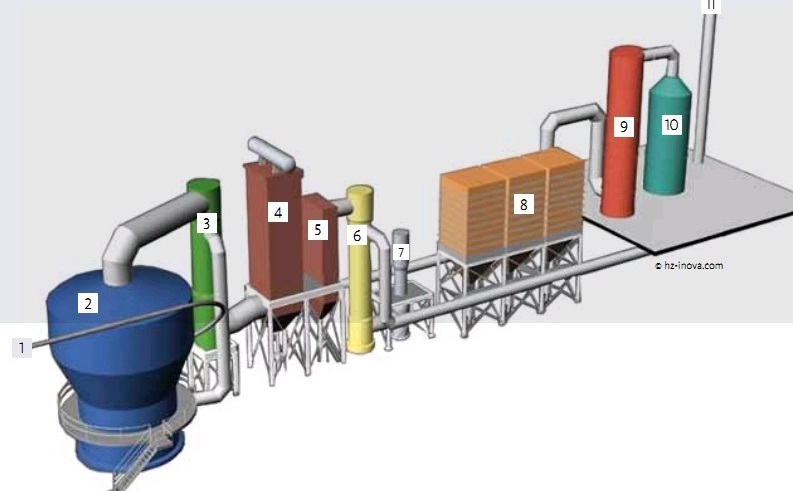
Рис.1. Схема сжигания отходов Hitachi Zosen
1- Топливоподача, 2 - Топка Inova, 3 - Первичный воздухонагреватель, 4 - Котел, 5 - Экономайзер, 6 - Вторичный теплообменник, 7 – Башенный угольный адсорбер, 8 - Тканевый фильтр, 9 - Мокрый скруббер, 10 - Мокрый электростатический осадитель, 11 - Дымовая труба
В ОВОС рассматриваются альтернативные варианты реализации проекта МСЗ и среди них вариант пиролиза. Данный вариант был исключен из рассмотрения на основании того утверждения, что он не оправдывает себя на смешанном потоке ТКО переменного состава.
Если характеризовать данный метод с точки зрения экологии, то следует обратить внимание на следующие моменты:
- проведение процесса пиролиза при температурах 400÷500°С и отсутствии кислорода исключает возможность синтеза диоксинов и окисления тяжелых металлов, и, соответственно, выход их из реактора;
- при сжигании газообразных и жидких продуктов пиролиза в горелках образование оксидов азота происходит в гораздо меньших концентрациях, чем при слоевом горении твердого топлива, что обусловлено конструкцией горелок и организацией процесса горения в них;
- при горении газообразных и жидких продуктов пиролиза не образуется летучая зола и шлаки ввиду их низкой зольности;
- нейтрализация основного количества кислых газов в продуктах пиролиза происходит непосредственно в реакторе за счет их связывания гидроксидом кальция, добавляемым к сырью;
- образующийся при сжигании газообразных и жидких продуктов пиролиза оксид серы связывается на стадии очистки дымовых газов щелочными реагентами в мокром скруббере;
На первом этапе внедрения технологии низкотемпературного пиролиза твердый остаток пиролиза, содержащий все минеральные компоненты, поступающие в реактор с сырьем, предполагается захоранивать на полигоне. Для снижения класса опасности твердого остатка пиролиза, после выгрузки из реактора он подвергается магнитной сепарации и классификации с целью извлечения из него электронных компонентов, элементов питания и других источников тяжелых металлов, попавших в «хвосты» на стадии сортировки. В последующем твердый углистый остаток будет подвергаться газификации с целью получения дополнительной тепловой и электрической энергии и снижения нагрузки на полигон.