Комплекс пиролизной утилизации углеродсодержащих отходов с четырьмя реакторами - КПУ-НП-4
КПУ-НП-4 предназначен для глубокой переработки "хвостов" сортировки твердых коммунальных отходов, обезвоженных канализационных илов, отходов птицеводства, животноводства, растениеводства и других видов твердых углеродсодержащих материалов методом низкотемпературного пиролиза в реакторе барабанного типа.
Комплекс состоит из линии предварительной мусоросортировки, участка дробления и накопления "хвостов" сортировки, четырех реакторов низкотемпературного пиролиза, двух блоков очистки и конденсации парогазовой смеси, котла-утилизатора негорючих газов, блока очистки дымовых газов, системы комплексной многоступенчатой очистки пирогенной воды.
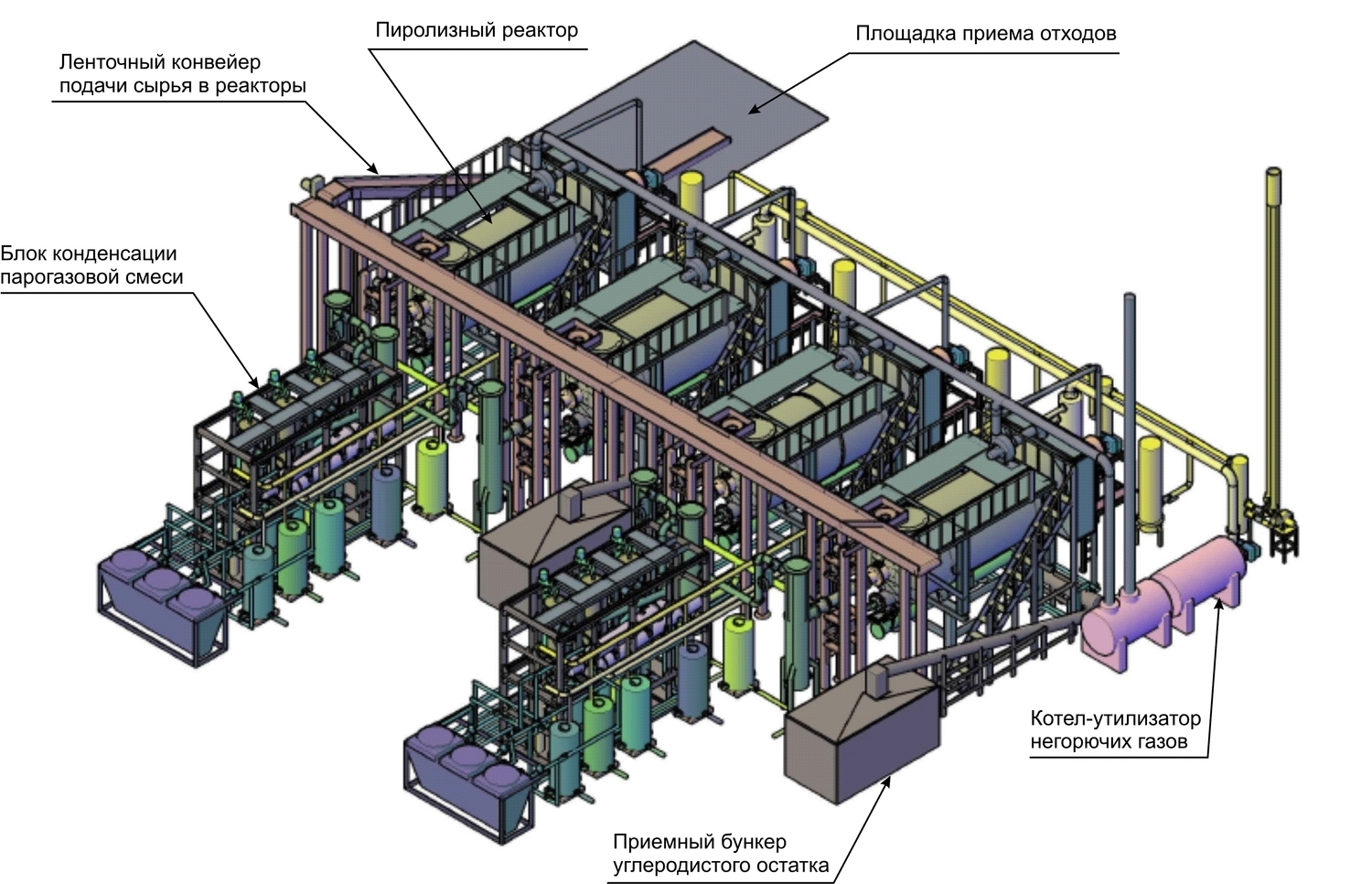
Из твердых коммунальных отходов предварительно извлекают крупногабаритный мусор, мелкую фракцию (до 70 мм), вторсырье, металлы, стекло, хлорсодержащие компоненты (ПВХ материалы). «Хвосты» сортировки измельчают в дробилке для получения фракции не более 150-200 мм.
Процесс термической деструкции - расщепление на твердую и газовую фазы происходит при постоянном вращении реактора. Теплопередача от теплоносителя происходит через стенки внутренних труб контура нагрева реактора, что повышает тепловой КПД реактора. При этом постоянное ворошение сырья способствует эффективным тепломассообменным процессам. Углеродсодержащий твердый остаток в результате получается мелкодисперсным и практически без запаха.
Реактор пиролиза барабанного типа является инновационной разработкой. Горелочное устройство реактора вынесена за пределы реакционной зоны. Внутренний контур обогрева рабочего объема реактора выполнен в виде горизонтально и радиально расположенных труб различного диаметра. Обогрев дымовыми газами осуществляется косвенным способом. Это позволяет избежать локальных зон перегрева сырья и преждевременного наступления пиролизных мини-процессов в местах соприкосновения сырья с жаровой трубой реактора на стадии сушки.
Блок конденсации содержит узел грубой очистки парогазовой смеси (ПГС) от твердых частиц, контур конденсации пара на стадии сушки, контур конденсации ПГС на стадии пиролиза. КПУ-НП-4 содержит два блока конденсации - основной и резервный.
Процесс переработки твердых коммунальных отходов представляет собой непрерывный процесс, при котором сырье («хвосты» ТКО) подается в бункер промежуточного хранения, откуда периодически загружается в один из реакторов, где подвергается термическому воздействию в бескислородной среде.
Комплекс обеспечивает термическую деструкцию твердого углеродсодержащего сырья при температурах до 450°С без доступа кислорода с получением пиролизного газа, жидких углеводородных фракций, твердого углеродсодержащего материала. Побочным продуктом является пирогенная вода, объем которой зависит от исходной влажности сырья.
Технологическая схема работы комплекса представлена как циклично-непрерывный процесс, включающий последовательно-параллельную работу реакторов со следующими повторяющимися стадиями:
- конвейерная подача сырья и загрузка в реактор закрытым шнековым способом;
- сушка сырья в реакторе до влажности 10-12 % при температурах 120-150°C с отведением парогазов в блок конденсации и разделением на поверхностную (капиллярную) воду и негорючие газы;
- термическая деструкция (пиролиз) сухого сырья без доступа кислорода при температурах 300 - 450°C с разделением парогазовой смеси на жидкие углеводородные фракции, пирогенную воду и горючие газы;
- выгрузка из реактора горячего углеродсодержащего остатка закрытым шнековым способом с одновременным охлаждением сухим способом до температуры не выше 150°C.
Конвейерная линия обеспечивает подачу сырья к каждому реактору. Загрузка осуществляется шнеком, расположенным внутри реактора, с периодическим проворотом реактора и подпрессовкой загруженной массы до плотности 400 кг/м3, что составляет 10 тонн для рабочего объема реактора 25 м3. Время технологического цикла одного реактора составляет 24 часа. Циклы работы реакторов смещены относительно друг друга на 6 часов. Поэтому КПУ-НП-4 перерабатывает в сутки 40 тонн сырья.
Стадия сушки сырья в реакторе протекает при температурах, исключающих термическую деструкцию органических веществ и получение углеводородных соединений. Образуемые при нагреве отходов парогазы дурно пахнут и не горючи. При охлаждении в блоке конденсации они разделяются на воду и неконденсируемую негорючую газовую смесь, которая направляется на обезвреживание в пламя горелки котла-утилизатора. Вода содержит вредные компоненты, требующие нейтрализации перед сбросом воды в канализацию или для использования ее в технических целях.
За стадией сушки следует стадия пиролиза, которая наступает с появлением горючих газов при температурах выше 300°С. В парогазах присутствует большое количество углеводородов, остатки пирогенной воды, углекислого газа, оксида углерода СО. При охлаждении парогазов конденсируемая часть углеводородов переходит в жидкие топливные продукты с одновременным разделением на фракции по заданным температурам кипения (конденсации).
Неконденсируемые горючие газы используются для питания горелок реактора и котла-утилизатора.
Для увеличения эффективности тепломассообмена веществ осуществляется постоянное ворошение сырья путем вращения реактора. При повышении давления в реакторе более 0,5 кгс/см2 избыток газов отводится в аварийную магистраль факельного дожига газов.
С прекращением образования пиролизных газов начинают выгрузку углеродистого остатка закрытым шнековым способом. При перемещении твердого остатка по наружному шнековому транспортеру его охлаждение происходит сухим способом через водяную рубашку корпуса шнека-охладителя.
Горючие газы в процессе пиролиза поступают в газораспределительную сеть комплекса и используются в первую очередь для работы горелок реакторов. Выход горючих газов составляет 40-60% от массы сухого сырья и зависит от морфологического состава перерабатываемых отходов. Большое количество газа получается при переработке отходов из полиэтилена, пластика, пластмассы.
Применяемый в технологическом процессе способ управляемой конденсации парогазовой смеси позволяет получать топливные фракции с различными диапазонами температур кипения, например, от 300°C и выше, от 300 до 180°C, ниже 180°C. За один производственный цикл выделяется топливо трех видов, по своим характеристикам аналогичное мазуту, солярке и бензину. Общий выход топливных фракций при переработке ТКО составляет 20-40% от массы сухого сырья и зависит от состава отходов. Например, резиносодержащие отходы значительно увеличивают количество жидких фракций.
После цикла пиролиза в реакторе остается порошкообразная углистая масса. Зольность твердого остатка (количество минеральных элементов) зависит от морфологического состава ТКО и составляет, в среднем, 20%.
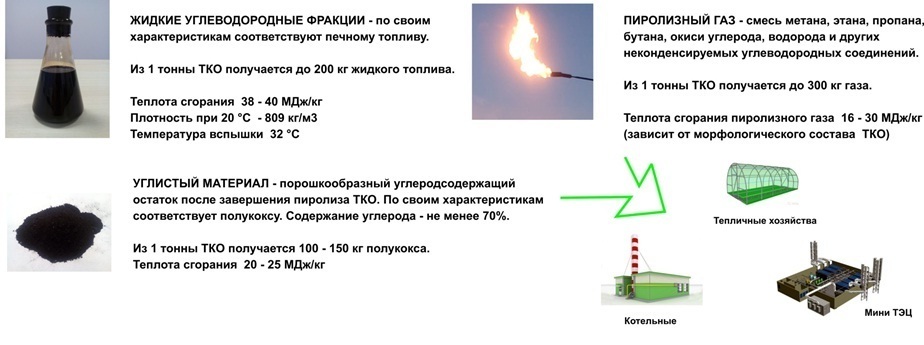
Предлагаемая технология низкотемпературного пиролиза органической массы отходов без доступа кислорода экологически безопасна и давно применяется за рубежом для получения альтернативных видов топлива. Оригинальные конструкторские решения узлов комплекса обеспечивают соблюдение санитарно-гигиенических, противопожарных, экологических нормативов, действующих на территории РФ. Производственный процесс переработки отходов исключает их непосредственное сжигание, характерное для мусоросжигательных заводов. Получаемые жидкие топливные фракции, углеродсодержащий твердый остаток и пиролизный газ используются как топливные продукты в парогенераторах (паровых котлах) мини-ТЭЦ для выработки электрической энергии на паротурбинной энергетической установке. Тепловая энергия отработавшего пара после турбины направляется в систему теплоснабжения промышленных или коммунально-бытовых потребителей.