Конструктивные решения для технологии быстрого пиролиза
Сушка и измельчение органического сырья.
Термохимическое разложение каждой частицы органического сырья на молекулярном уровне (быстрый пиролиз) проходит эффективно при выполнении следующих основных условий: размер частицы не более 1-2 мм, влажность сырья до 10%, температура предварительного нагрева порядка 150 оС, применяется эффект «термоудара» при входе сырья в камеру пиролиза.
При естественной влажности сырья до 25 – 30 % используется относительно не сложное по конструкции оборудование сушки-измельчения на основе молотильно-дробильных машин. Основным принципом работы данного оборудования является растирание и разбивание частиц за счет действия рабочих органов, а также самоизмельчение частиц в результате их соударений в потоке воздуха. При этом часть механической энергии переходит в тепло, за счет которого и происходит высушивание сырья. Дополнительный подвод тепла от разогретого пиролизного реактора обеспечивает повышение температуры сырья до заданных значений 120 – 150 ºС.
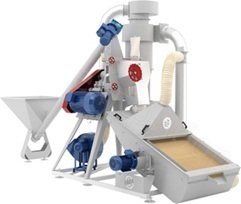
Такие виды влажного сырья, как канализационный ил, куриный помет, свиной навоз и др., требуют применения более сложных технологий и конструктивных решений, например, сушка в турбовихревом потоке.
Сушилка представляет собой газодинамическую машину, принцип работы которой основан на эффекте Ранка. Сырой материал под действием мощного вихревого потока превращается в тонкодисперсную аэрозоль, где вещество передает свою влагу воздуху. Данная технология сушки представляет собой процесс осушения (сублимирования) в диапазоне температур от 25 до 80 ºС и измельчения исходного материала влажностью до 98% на однородный порошкообразный материал, влажностью до 10%.
Оборудование ЭКПУО для участка подготовки сырья проектируется и изготавливается применительно к каждому виду углеродосодержащего сырья с учетом основных свойств и характеристик исходного материала: влажность, насыпная плотность, физическая структура частиц и др.
Организация пиролизных реакций.
Термохимическая деструкция частиц органического сырья начинается в реакторе под действием эффекта «термоудара» и продолжается в диапазоне температур 700-900 °С в условиях высокоскоростного тепломассообмена. Данная технология может реализовываться с применением следующих пиролизных реакторов:
1. Абляционный реактор - нагрев углеродосодержащих частиц происходит за счет передачи тепловой энергии через наклонную нагретую поверхность, по которой перемещается сырьё под действием силы тяжести.
2. Вихревой реактор - используется способ аэродинамической организации горящего вихря, обеспечивающего управление перемешиванием газовой взвеси частиц.
Основное ограничение на конструкцию пиролизного реактора накладывает требование высокого уровня теплопередачи. Для абляционного реактора передача тепла в камеру пиролиза осуществляется через стенку и является основным ограничением производительности. Данное решение применяется для малых объемов переработки сырья (до 500 кг/час).
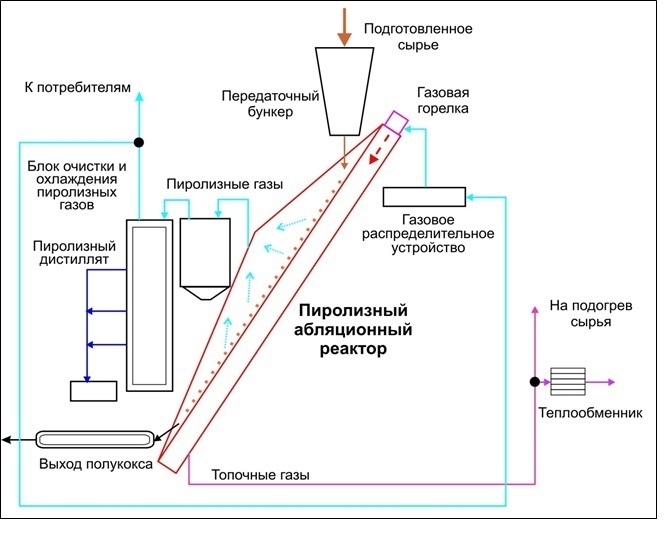
На схеме показан принцип работы абляционного реактора. Нагретое и измельченное сырье тонким слоем подается в разогретую камеру пиролиза без доступа воздуха. Образовавшийся пиролизный газ отводится в блок очистки и охлаждения газов таким образом, чтобы в камере пиролиза поддерживалось давление, близкое к атмосферному. Небольшая часть газа используется для работы газовой горелки, остальной газ, охлажденный и очищенный от смолей и угольной пыли, направляется к потребителям. Мелкодисперсный уголь с зольным остатком и пиролизный дистиллят охлаждаются и выводятся в приемные устройства для дальнейшей переработки.
Нагрев сырья в камере пиролиза осуществляется в условиях механоактивации за счет организованного трения органических частиц о стенки камеры пиролиза. Данный способ позволяет постоянно удалять с поверхности частицы сырья образующийся уголь, что значительно ускоряет протекание реакций пиролиза. Объясняется это тем, что увеличивающийся по толщине в ходе процесса термической переработки слой угля создает нарастающее по времени сопротивление теплоподводу и отводу продуктов разложения. Это, в свою очередь, снижает скорость процесса термической переработки, ведет к вторичному разложению образующихся продуктов пиролиза и исключает стабильность процесса пиролиза и свойств получаемых продуктов пиролиза.
Пиролизной вихревой реактор в отличие от абляционного, имеет более сложную технологию организации теплообмена за счет вихревого потока и позволяет перерабатывать большие объемы сырья. Сырье тангенциально подается в камеру пиролиза, в которой специальным образом организован разогнанный высокотемпературный поток тонкодисперсного сырья. Вихревой поток формирует структуру течения с высоким радиальным градиентом статического давления, что активизирует процессы смесеобразования и термической деструкции сырья.
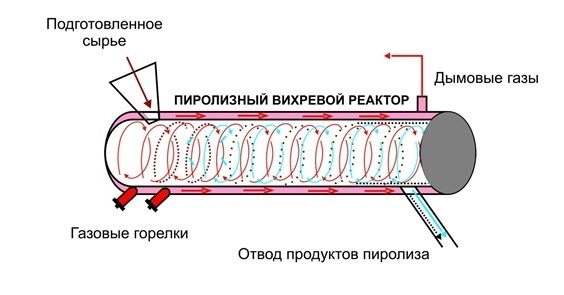
В основу создания вихревой пиролизной камеры положены некоторые из свойств сильно закрученных потоков вязкого сжимаемого газа. Среди этих свойств можно выделить:
- высокий радиальный градиент статического давления;
- сильно развитая анизотропная турбулентность;
- интенсивные высокочастотные акустические колебания;
- высокая степень электризации частиц внутри вихревой камеры.
Наличие высокоразвитой анизотропной турбулентности способствует наиболее полному тепломассообмену, что приводит к увеличению скорости пиролизных реакций. Тангенциальный подвод измельчённых органических частиц в камеру пиролиза также увеличивает скорости химических реакций. В вихревом закрученном потоке частицы интенсивно встряхиваются и сталкиваются друг с другом, что приводит к развитию деформаций, к разрушению частиц и к трению между частицами. Разрушение и трение, в свою очередь, вызывают кратковременное возбуждение атомов и молекул в приповерхностном слое вещества с образованием свободных радикалов. Свободные радикалы имеют один или два неспаренных электрона, что способно значительно усилить их реакционную способность и ускорить протекание химических реакций.
В результате взаимодействия высокотемпературных потоков продуктов пиролиза с частицами сырья возникают экзотермические реакции с выделением теплоты, пиролизного газа и углистого вещества, которое вновь подвергается процессу газификации. Углерод углистого вещества окисляется до окиси углерода, а водород частично используется в реакциях синтеза низших углеводородов, частично – в реакции окисления кислородом, с образованием водяного пара, который, реагируя с углеродом, также синтезирует углеводороды. В результате протекания химических реакций пиролизный газ обогащается горючими компонентами. В состав горючих компонентов входят окись углерода, низшие углеводороды и водород, увеличивая удельную теплоту сгорания пиролизного газа. Необходимую максимальную температуру в реакционной зоне поддерживают путём регулирования расхода газа в горелочных устройствах пиролизного реактора.
Образовавшийся пиролизный газ отводится в многоступенчатую систему очистки и охлаждения газов. На первом этапе газ очищается от смолей и пыли без принудительного охлаждения с минимальным образованием пиролизного дистиллята. На следующих ступенях очистка газа осуществляется с охлаждением в заданных диапазонах температур, и при достижении температуры 450 °С пиролизный газ подвергается резкому охлаждению (за доли секунды) до 200 °С для предотвращения образования вредных компонентов диоксинов.