Пиролизный вихревой реактор
Конструкция пиролизного вихревого реактора должна обеспечивать высокую эффективность процесса пиролиза углерод- и углеводородосодержащих материалов (твердых дисперсных, жидких и газообразных) во взвешенном динамическом состоянии вихревого закрученного потока с целью получения качественных углеводородных продуктов (предпочтительно горючих неконденсируемых газов). Техническая задача решается тем, что реактор имеет горизонтальную камеру пиролиза цилиндрической формы с тангенциально расположенным в начале камеры патрубком (2) ввода потока газовзвеси и тангенциально ориентированным патрубком (3) отвода продуктов пиролиза в конце камеры, размещенном на расстоянии трех диаметров камеры пиролиза от плоскости входа газовзвеси в реактор, что обеспечивает создание и поддержание сильнозакрученного вихревого потока газовой и твердой фаз по всей длине камеры. При этом торцевые стенки камеры пиролиза, осевые линии патрубка ввода потока газовзвеси и отводного патрубка параллельны и отклонены от вертикальной плоскости на угол 5-10 градусов для создания поступательного движения закрученного потока.
Температурный режим в камере пиролиза поддерживается регулированием подачи пиролизного газа в газовые горелки внешнего и внутреннего тепловых контуров реактора. Внешний тепловой контур (4) представлен объемом между стенками камеры пиролиза и цилиндрического корпуса реактора, внутри которого соосно размещена камера пиролиза (1). Внутренний тепловой контур представлен трубой (7), расположенной соосно внутри камеры пиролиза и проходящей по всей ее длине. Внешний тепловой контур содержит патрубок (5) подвода тепла от газовой горелки (условно не показана) и патрубок (6) отвода дымовых газов. Объемы тепловых контуров и камеры пиролиза изолированы друг от друга.
В первой половине камеры пиролиза соосно с трубой внутреннего теплового контура расположен щелевой кожух-завихритель (8) потока газовзвеси на длине от 0 до 30% расстояния между торцевыми стенками камеры пиролиза, соединенный с патрубком (9) отвода части пиролизного газа на рециркуляцию. При этом щели кожуха-завихрителя расположены так, чтобы придавать потоку газовзвеси вращательно-поступательное движение вокруг трубы, которая стабилизирует закрученный вокруг нее вихревой поток газовой и твердой фаз продуктов пиролиза.
Ось реактора может отклоняться в вертикальной плоскости относительно горизонта в пределах угла от «минус» 20-ти градусов до «плюс» 20-ти градусов с вершиной в точке пересечения оси реактора с его задней торцевой стенкой. Положение оси реактора регулируется механизированным способом для достижения оптимального времени пребывания частиц сырья в реакционной зоне камеры пиролиза. В частности, данное условие характерно для сырья повышенной дисперсности.
Пиролизный вихревой реактор работает следующим образом. Заданный температурный режим в камере пиролиза (1) поддерживается за счет регулирования подачи тепла от газовых горелок внутреннего и внешнего тепловых контуров реактора. Поток газовзвеси, состоящий из частиц сырья и рециркуляционного пиролизного газа, тангенциально направляется в камеру пиролиза через патрубок (2), закручиваясь по спирали вокруг щелевого кожуха-завихрителя (8) и трубы (7) внутреннего теплового контура. В создании вращательно-поступательного движения потока газовзвеси также участвуют отсасывающие силы тяги, тангенциально направленные через щели кожуха-завихрителя (8) и вдоль оси патрубка (3) отвода продуктов пиролиза. Заданное разряжение в реакционной зоне обеспечивается регулированием производительности вытяжного устройства, отводящего газовую и твердую фазы из камеры пиролиза.
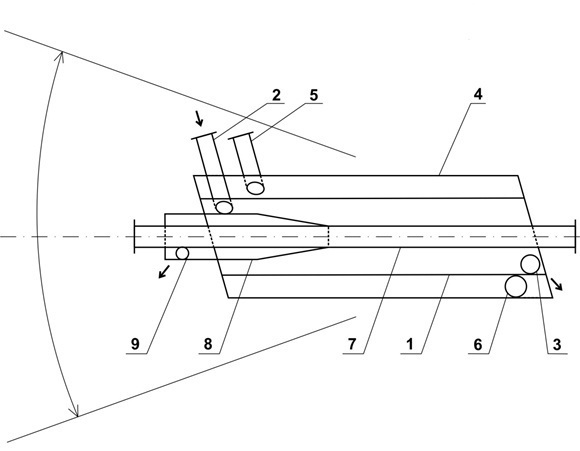
Преимуществом разработанного реактора является достижение высокоскоростной глубокой термохимической деструкции частиц сырья в сильнозакрученном вихревом потоке. Кроме того, конструкция и принцип работы реактора позволяют осуществлять конверсию разных видов сырья: твердых дисперсных, жидких и газообразных.
Пиролизный реактор является главным элементом в устройстве для переработки углеродсодержащего и/или углеводородсодержащего сырья в энергию и топливо. Получение качественных углеводородных продуктов во многом зависит от параметров и условий процесса воздействия на газовую и твердую фазы продуктов пиролиза после выхода из реактора, что связано с конструкцией пиролизной установки.