Описание технологических процессов производства
Технология переработки органических материалов способом быстрого пиролиза является универсальной для любого вида углеродосодержащего сырья. В пиролизный реактор поступает подготовленное сырье – высушенное и измельченное до фракции не более 1-2 мм. С точки зрения подготовки самыми простыми являются такие виды сырья, как древесные опилки, лузга подсолнечника, торф и др. Более сложная технология подготовки требуется для сырья с высокой влажностью и наличием различных включений – это иловые осадки сточных вод, навоз, куриный помет, нефтешламы. Для каждого вида сырья проектируется соответствующее оборудование сушки и измельчения. Предварительно, как правило, применяется сепарирование и удаление металлических предметов, камней и прочих элементов.
На участке предварительной подготовки после удаления механической примеси сырье загружается в приемный бункер-накопитель и далее подается в агрегат сушки-измельчения, где происходит удаление влаги, измельчение частиц до фракции не более 1-2 мм и нагрев до температуры порядка 150°С. Частицы сырья должны иметь небольшие размеры, чтобы обеспечить высокую производительность и эффективность технологического процесса.
При использовании сырья с влажностью более 30% предусматривается отвод паровоздушной смеси в процессе сушки сырья. Измельченное и нагретое сырье поступает в промежуточный бункер, откуда подается в пиролизный реактор. Управление подачей сырья осуществляется в автоматическом режиме в зависимости от заданной производительности установки.
Термическое разложение органического сырья в пиролизном реакторе происходит в режиме быстрого пиролиза. На начальном этапе для запуска реактора используется баллонный газ. Перед подачей сырья реактор разогревают до температуры ~ 750°С. В дальнейшем для поддержания температурного режима работы реактора используется собственный пиролизный газ. В процессе быстрого пиролиза происходит выделение тепла (экзотермическая реакция), поэтому для поддержания заданного температурного режима подачу газа в горелки реактора уменьшают. Пиролизный реактор в режиме экзотермии требует минимального подвода тепловой энергии.
Пиролизный газ. Поступающие в пиролизный реактор частицы сырья получают мгновенный термоудар без доступа кислорода при температуре 700 – 900°С, в результате чего на молекулярном уровне происходит разрыв углеводородных цепочек и образуется пиролизный газ. Термическое разложение органического сырья представляет собой сложный процесс, который можно представить как ряд протекающих последовательно и параллельно химических реакций с образованием большого числа продуктов. Первичную реакцию пиролиза биомассы (БМ) можно представить следующим образом:
БМ + тепло = СО + СО2 + Н2 + Н2О + СН4 + СnНm + С (полукокс) + смолы
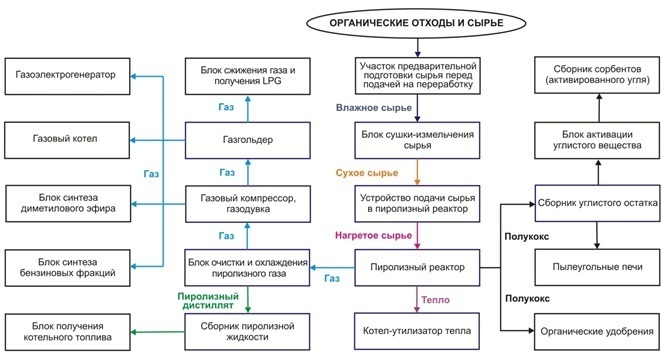
Состав газа зависит от вида сырья и параметров процесса. Процесс пиролиза протекает при низком давлении, что обеспечивается непрерывным принудительным отводом образующихся газов из реактора. Пиролизный газ поступает в систему очистки от смолей и угольной пыли и далее проходит стадию конденсации. Очищенный и охлажденный газ направляется к потребителям – для сжигания в печах, в газоэлектрогенераторную установку для производства электроэнергии или закачивается под давлением в резервную емкость для хранения газа (газгольдер).
Полукокс. Продуктом быстрого пиролиза является мелкодисперсное углистое вещество с высоким содержанием углерода (полукокс), которое после охлаждения фасуется, а затем используется по назначению. Порошковый полукокс имеет развитую поверхность микропор, достигающую 400‑600 м2/г, и высшую калорийность в пределах 6000‑7000 ккал/кг. Полукокс можно использовать в качестве пылеугольного топлива для сжигания в печах. Методом активации из него можно получать сорбенты и активированные угли. Кроме того, отличные результаты показало использование получаемого полукокса для увеличения плодородности земель в сельском хозяйстве.
Синтетическая нефть. Выводимый из пиролизного реактора горячий газ проходит ступенчатое охлаждение, в результате чего получается пиролизный дистиллят, который представляет собой густую черную смолянистую жидкость. В состав жидких продуктов пиролиза входят ароматические углеводороды, алканы, алкены и множество других химических элементов. Пиролизная жидкость отправляется на дальнейшую химическую переработку для получения различных видов топлива или выделения ценных химических элементов.
Сжиженный углеводородный газ. Очищенный и охлажденный пиролизный газ закачивается под давлением в резервную емкость (газгольдер), что приводит к сжижению пропан-бутановых фракций. В нижней части газгольдера образуется сжиженный газ (LPG), а в верхней части скапливаются легкие фракции – метан, водород, монооксид углерода и пр. Таким образом, появляется возможность сжиженные углеводородные газы перекачивать в отдельные емкости и использовать в качестве топлива в двигателях внутреннего сгорания и для бытовых нужд.
Диметиловый эфир. Пиролизный газ содержит монооксид углерода и водород, что позволяет на основе известной технологии каталитического синтеза получать диметиловый эфир. Легкие фракции пиролизного газа (синтез-газ) отбираются из газгольдера и направляются в синтез-реактор, где под давлением 5 – 18 кгс/см2 и температуре 280 – 300°С в присутствии катализатора происходит конверсия синтез-газа в диметилэфир, который после охлаждения закачивается в резервуар.
Бензин. Из тяжелых фракций пиролизного газа способом каталитического синтеза также можно получать жидкое топливо, по характеристикам близкое к маркам бензина А-92, А-95.
Тепловая энергия. Выделившаяся тепловая энергия от топочных газов реактора и в результате охлаждения продуктов пиролиза направляется на цели отопления и горячего водоснабжения или нагрев различных технологических сред с использованием специального теплообменного оборудования.