Сравнительная оценка мусоросжигательного завода по технологии колосникового сжигания и мусороперерабатывающего завода по технологии пиролиза
Краткая характеристика технологических решений мусоросжигательного завода мощностью 700 тысяч тонн ТКО в год (д. Могутово Московской области):
- принятая технология обезвреживания ТКО – сжигание на колосниковой решетке;
- основное оборудование: котел паровой с колосниковой решеткой – 3 ед.; паровая турбина типа К, генератор паровой турбины, конденсатор, трехступенчатая система газоочистки – 3 ед.;
- котлы рассчитаны на удельную теплоту сгорания топлива 9100 кДж/кг. При поступлении ТКО с теплотой сгорания ниже 6000 кДж/кг в работу будут включаться вспомогательные горелки газового топлива (природный газ). Расход природного газа на один котел составит 4560 нм3/час, на три котла – 13680 нм3/час (при цене природного газа за 1000 м3 – 6000 руб. затраты на работу 3-х котлов составят 82080 руб./час или 59 097 600 руб. в месяц);
- в принятой технологии МСЗ принято, что сжиганию будут подвергаться отходы, прошедшие предварительную сортировку на мусороперегрузочных станциях. Однако не понятно, будут ли отбираться на этих станциях высоковлажные мелкие фракции отходов с дальнейшим их компостированием. В противном случае теплота сгорания ТКО может составить менее 6000 кДж/кг. При влажности 50% и зольности 18% теплота сгорания ТКО составляет 5850 кДж/кг. В осенне-зимний и зимне-весенний сезоны потребуется постоянно использовать горелки газового топлива, что увеличит себестоимость получаемой электроэнергии.
- сжигание отходов происходит на решетке при температуре от 850 до 1000 °С, шлак падает через желоб в воду разгружателя шлака и охлаждается, водяной пар поднимается в камеру сжигания;
- в принятой технологии МСЗ шлак составляет от 25 до 30% от сожженного количества ТКО по весу и согласно ОВОС представляет собой инертные отходы IV класса опасности. Однако при технологии колосникового сжигания шлак, образуемый при сжигании смешанных ТКО, нельзя отнести к инертным отходам, так как в нем неизбежно будут присутствовать соединения тяжелых металлов.
- образующиеся при сжигании ТКО газы с температурой 900 °С поступают в паровой котел. Получаемый в котле перегретый пар под давлением от 60 до 70 бар и температурой 430 °С направляется на турбогенератор мощностью 70 МВт, который преобразует энергию пара в электричество.
- очистка образующих при сжигании ТКО газов проводится в три этапа: в котле от оксидов азота; в реакторе, где дымовые газы вступают во взаимодействие с реагентами (гашеная известь и активированный уголь) для удаления кислотных газообразных загрязняющих веществ, органических загрязняющих веществ, тяжелых металлов, вторичных диоксинов и фуранов; в рукавном фильтре оседает летучая зола, пыль, частицы активированного угля, чистка которых происходит автоматической пульсацией воздуха, подаваемого от компрессорной станции.
- после очистки дымовые газы удаляются через трубу высотой 98 метров в атмосферу. В трубе установлен газоанализатор, который постоянно контролирует содержание загрязняющих веществ в уходящих газах. Однако не понятно, содержание каких именно вредных веществ контролирует газоанализатор. И каким образом контролируются в дымовых газах диоксины, фураны, сажа, пыль.
- в п. 2.6. ОВОС сказано, что на заводе ведется мониторинг состава дымовых газов на всех ступенях очистки газов в реальном времени. Однако не сказано, какие именно показатели контролируются. Технологический партнер проекта берет на себя финансовые гарантии того, что выбросы загрязняющих веществ на выходе из дымовой трубы соответствуют законодательным нормам. Насколько весомы эти гарантии и какой механизм их реализации для покрытия экологического ущерба окружающей среде и экономического ущерба в случае остановки завода?
- в проекте МСЗ рассмотрены альтернативные варианты технологических решений (сжигание отходов в кипящем слое, пиролиз, газификация, плазменная газификация). В качестве наиболее распространенной и высокоэффективной выбрана технология сжигания на колосниковой решетке с применением современной технологии очистки дымовых газов. Однако проектом предусмотрена трехступенчатая сухая система очистки дымовых газов, когда в Швейцарии и других западных странах на МСЗ применяется пятиступенчатая система очистки дымовых газов, включая мокрую очистку в скрубберах.
- стоимость проекта МСЗ составляет более 30 млрд. рублей.
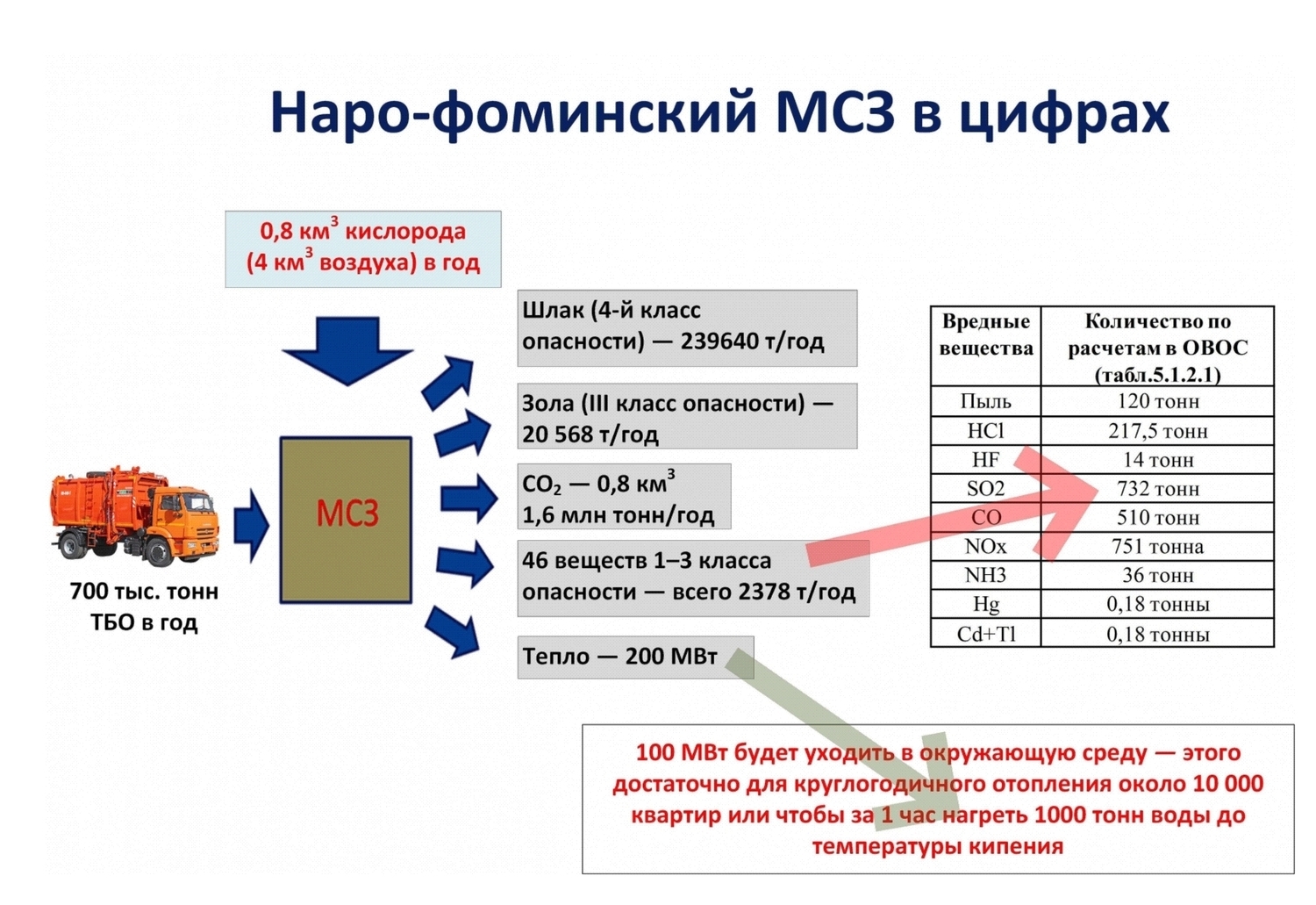
Краткая характеристика технологических решений проектируемого мусороперерабатывающего завода по технологии пиролиза:
- принятая технология обезвреживания ТКО – низкотемпературный пиролиз «хвостов» сортировки ТКО в реакторе барабанного типа. Из отходов предварительно должны быть отобраны непиролизуемые материалы (минеральные компоненты, ПВХ, другие хлорсодержащие материалы) и высоковлажные мелкие фракции (менее 70 мм).
- рабочий объем одного реактора – 25 куб.м., загрузка осуществляется шнековым способом с подпрессовкой, что обеспечивает массу пиролизуемого сырья в реакторе 10 тонн;
- пиролизный модуль содержит 4 реактора и 2 блока очистки и конденсации парогазовой смеси (далее «блок конденсации»). Один блок конденсации используется в качестве резервного на стадиях пиролиза в период проведения техрегламента или ремонта на оборудовании другого блока конденсации.
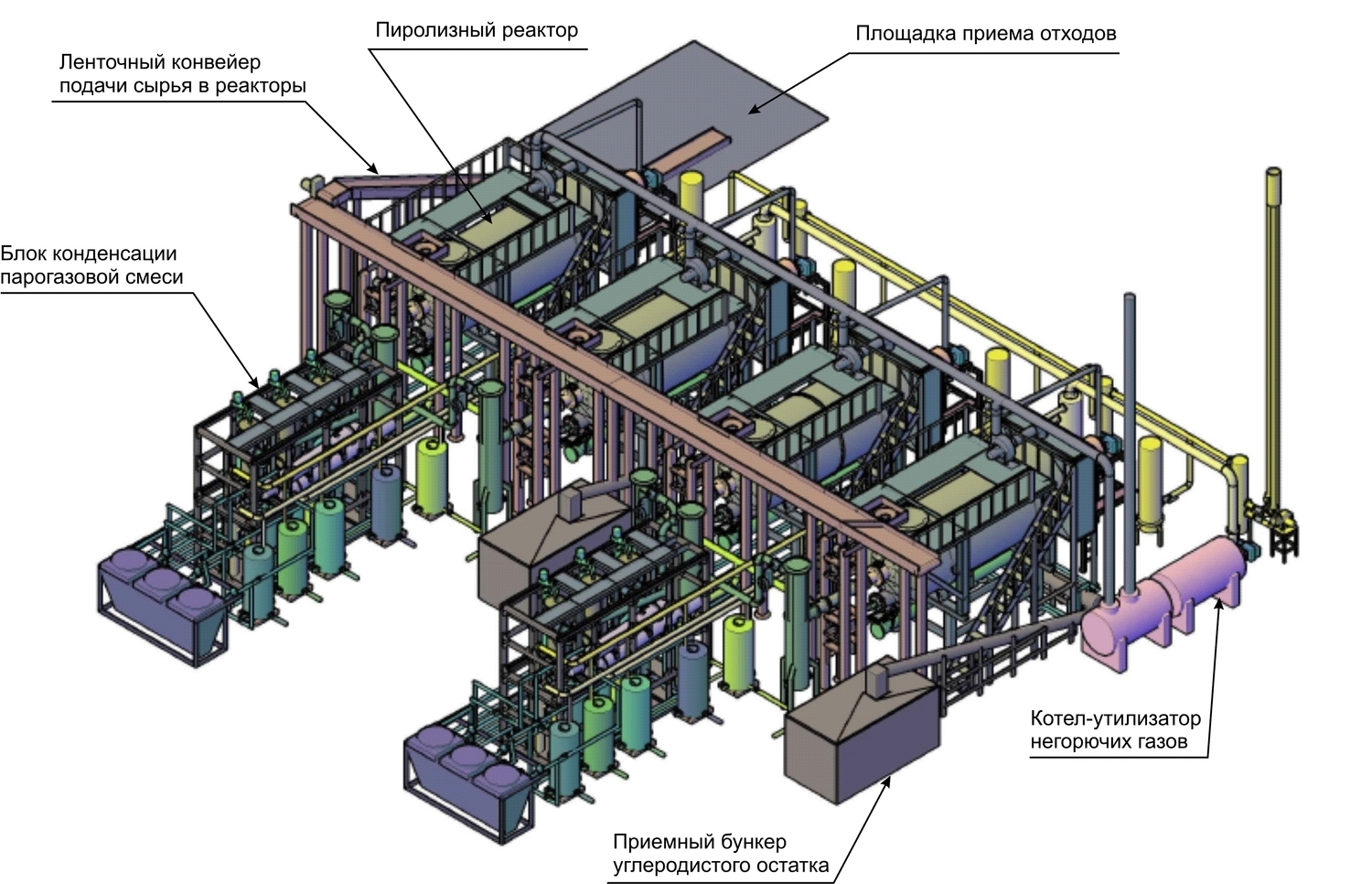
- технологический цикл одного реактора состоит из следующих стадий: загрузка отходов в реактор (2-3 ч), сушка (9-11 ч), предпиролиз (1-2 ч), пиролиз (5-6 ч), послепиролиз (2-3 ч), выгрузка твердого остатка (1-2 ч). Реактор работает в цикличном режиме. Горючие газы образуются на стадии пиролиза и используются для питания горелки реактора. Избыток газов подается в газовую распределительную сеть пиролизного модуля и используется для работы горелок других реакторов.
- реакторы запускаются последовательно, циклы реакторов сдвинуты по времени таким образом, чтобы контур пиролиза блока конденсации (3 скруббера для выделения из парогазов жидких углеводородных фракций и 1 конденсатор для пирогенной воды) был постоянно загружен парогазами за счет последовательного подключением к нему каждого реактора. Эта схема работы пиролизного модуля обеспечивает постоянную выработку модулем из 4-х реакторов горючего пиролизного газа.
- в случае не высокой калорийности пиролизного газа или его недостачи для устойчивой работы горелки реактора осуществляется подпитка горелочного устройства природным газом. Возможно также применение жидкотопливной (двутопливной горелки) для использования жидкого пиролизного топлива (аналог печного топлива).
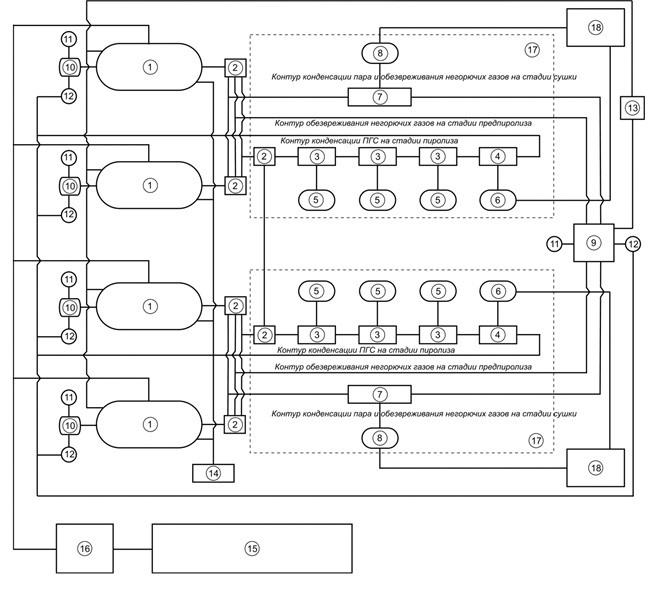
Рис.1. Блок-схема пиролизного модуля (КПУ-НП-4).
1 – реактор пиролиза; 2 – узел грубой очистки ПГС; 3 – скруббер с насадкой; 4 – конденсатор пирогенной воды; 5 – емкость для жидких углеводородных фракций; 6 – емкость для пирогенной воды; 7 – конденсатор-холодильник; 8 - емкость для сбора конденсата; 9 – котел-утилизатор с муфельной топкой; 10 –камера сгорания; 11 – жидкотопливная горелка; 12 – газовая горелка; 13 - скруббер очистки дымовых газов; 14 – приемный бункер углеродистого остатка; 15 – линия сортировки ТКО; 16 - участок дробления и накопления "хвостов" сортировки; 17 – блок конденсации ПГС; 18 – блок очистки конденсата.
- отсутствие доступа кислорода и низкие температуры пиролиза (300 – 450 °С) исключают образование диоксинов в процессе термической деструкции отходов. Большая часть растворимых органических загрязняющих веществ оседает в пирогенной воде, которая подвергается обеззараживанию с применением известных способов очистки производственных сточных вод. Пыль и сажа в дымовых газах практически отсутствует, так как в горелках сжигается пиролизный газ, прошедший трехступенчатую мокрую очистку в скрубберах. При сжигании в горелках жидкого пиролизного топлива взвешенных веществ в дымовых газах будет несколько больше. Очистка дымовых газов, образуемых при работе всех горелок пиролизного модуля, происходит в мокром скруббере с использованием гашеной извести в качестве реагента.
- на стадии предпиролиза и послепиролиза парогазовая смесь, образуемая в реакторе, обезвреживается огневым методом в пламени горелки котла-утилизатора;
- твердый углистый остаток выгружается из реактора сразу после стадии послепиролиза, беспылевым способом, с одновременным сухим охлаждением. При отсутствии в нем тяжелых металлов (что зависит от качества предварительности сортировки ТКО) углистый остаток можно использовать в качестве твердого топлива. В противном случае он требует захоронения на полигоне ТКО.
- пиролизные топливные фракции (пиротопливо) целесообразно использовать для выработки электроэнергии на паротурбинной установке. Полученную электроэнергию использовать на собственные нужды, а оставшуюся часть реализовывать по зеленому тарифу. Экотехнопарки, имеющие МПЗ по технологии пиролиза ТКО, могут быть полностью обеспечены собственной электроэнергией и теплом.
- модульный принцип строительства мусороперерабатывающего завода по технологии пиролиза позволяет проектировать разную мощность – от 40 тонн «хвостов» сортировки ТКО в сутки (13200 тонн в год) до 1280 тонн в сутки (400000 тонн в год) и более. В каждом регионе целесообразно строить один-два крупных МПЗ и несколько малых и средних заводов. На крупных МПЗ будет вырабатываться электроэнергия с использованием пиролизного топлива, получаемого на всех заводах региона.
- МПЗ по технологии пиролиза включает весь комплекс оборудования для переработки ТКО: сортировочные линии, участок компостирования мелкой фракции, пиролизные модули. ТЭЦ целесообразно проектировать электрической мощностью 6 МВт, работающей на жидком пиролизном топливе, что соответствует МПЗ мощностью 150 тысяч тонн ТКО в год.
Таким образом, предлагаемая технология пиролиза ТКО является экологичной и экономически эффективной, в отличие от технологии колосникового сжигания, так как:
1. Количество и объемы выбросов вредных веществ минимальные.
2. Капитальные затраты на строительство МПЗ меньше в 2 раза, чем на строительство МСЗ аналогичной мощности.
3. Операционные затраты МПЗ значительно меньше (не требуется внешних энергоносителей, стоимость обслуживания системы очистки дымовых газов на порядки ниже).
4. Технология пиролиза масштабируемая, что позволяет использовать ее как для малых, так и для крупных городов, а также для мобильных комплексов.
5. Жидкое пиролизное топливо – это альтернативный источник тепла и электроэнергии, получаемый из всех видов органических отходов и сырья.
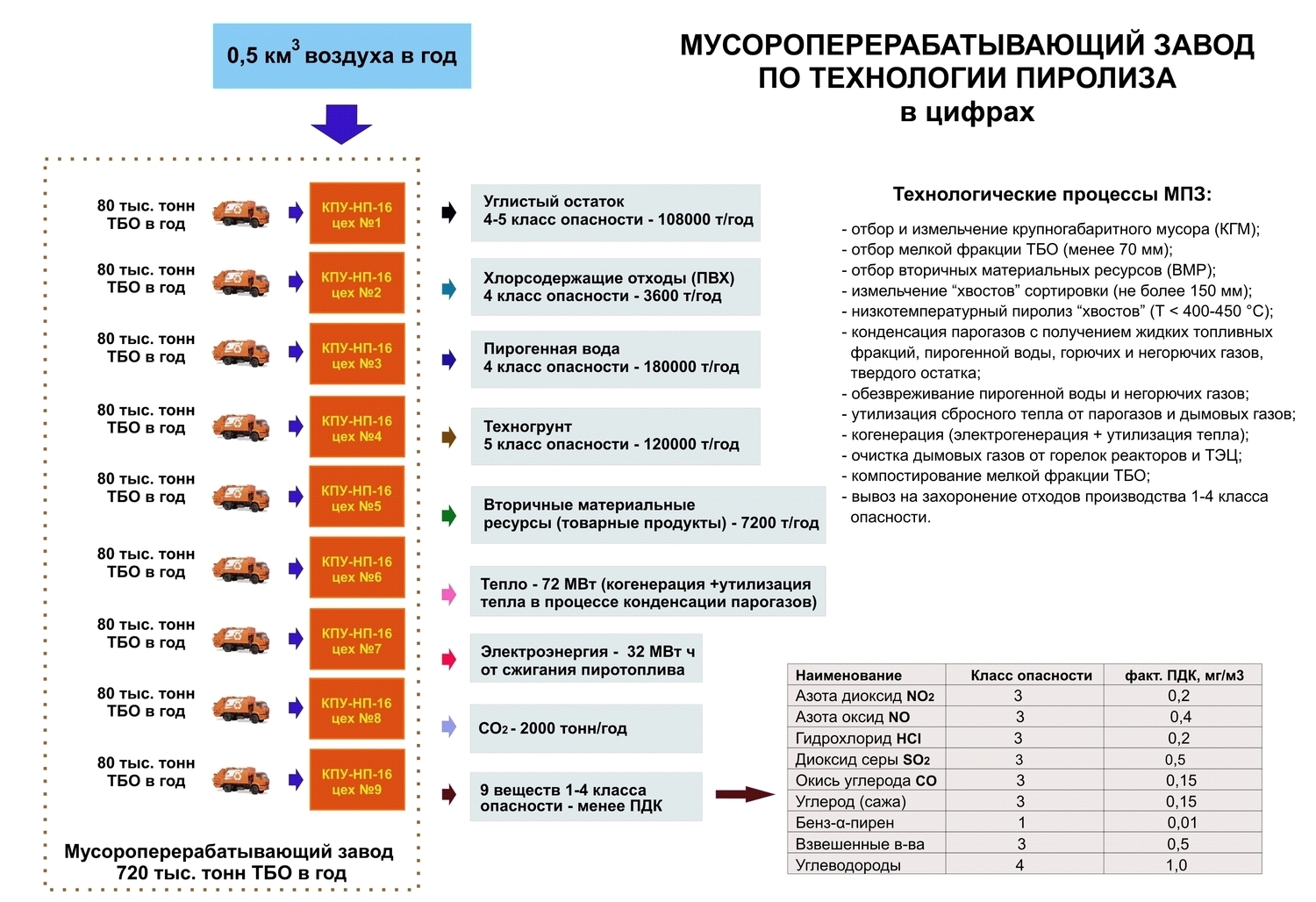